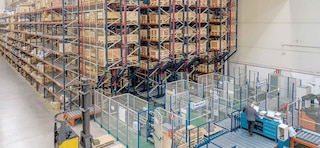
¿Qué es Lean logistics? La estrategia hacia la eficiencia
La metodología Lean logistics es una filosofía de gestión y organización de operaciones de origen japonés. Aplicar Lean Logistics a la cadena de suministro consiste en identificar y eliminar las actividades que no añaden valor para poder incrementar el flujo de productos, minimizando así los costos.
El concepto Lean se puede resumir con la máxima: “hacer cada vez más con menos” y esto se puede completar apuntando: menos esfuerzo, menos equipamiento, menos espacio, menos costos y menos tiempo.
Inicialmente, este conjunto de métodos, desarrollado por Taiichi Ohno en la empresa Toyota, se aplicó en el campo de la producción industrial, de ahí que se llamase Lean manufacturing.
Principios de la metodología Lean logistics
La Lean logistics tiene por objetivo reducir los costos logísticos poniendo énfasis en detectar y atajar aquellas tareas que no generan valor añadido al proceso. Como consecuencia, se logrará un acortamiento del tiempo de ciclo del pedido. Al final, se trata de una búsqueda constante de la eficiencia, que podemos dividir en varias fases o principios:
1. Identificar qué actividades añaden valor para el cliente
Gracias a herramientas como el Value Stream Map, este primer paso se concentra en evidenciar todas las tareas que componen un proceso concreto. Por ejemplo, en la bodega, las operaciones de picking se dividen en varias fases y cada una de esas fases se puede desgranar en más subprocesos.
2. Detectar los despilfarros y, a la vez, encontrar oportunidades de mejora
En logística los despilfarros muchas veces están relacionados con la pérdida de tiempo como veremos más adelante. La estandarización de tareas y el mantenimiento de la limpieza y el orden en la bodega son fundamentales para ejecutar esta etapa correctamente.
3. Crear un nuevo flujo de procesos optimizado
Se trata de diseñar un nuevo método de trabajo más eficaz en cuanto a tiempo dedicado y a calidad del servicio. Para ello, hay que suprimir las tareas innecesarias e identificadas como despilfarros.
Además de cambios organizativos, esta fase puede suponer ejecutar inversiones en nueva tecnología o sistemas que ayuden a eliminar esas etapas que están consumiendo tiempo extra sin aportar valor.
4. Optar por estrategias pull para minimizar el inventario
La tenencia de stocks determina gran parte de los costos logísticos. Frente a las estrategias push (empujar), que se basan en producir bajo una previsión de ventas, los métodos de producción pull (tirar) están centrados en atraer las ventas en primer lugar y responder a ellas suministrando el producto con agilidad.
5. Estandarizar los nuevos procesos y mantener el cambio en el tiempo
Para ello, hay que implicar y motivar a todos los trabajadores y facilitarles la formación adecuada para que puedan adquirir los nuevos hábitos y las tan necesarias habilidades que componen el llamado talento 4.0.
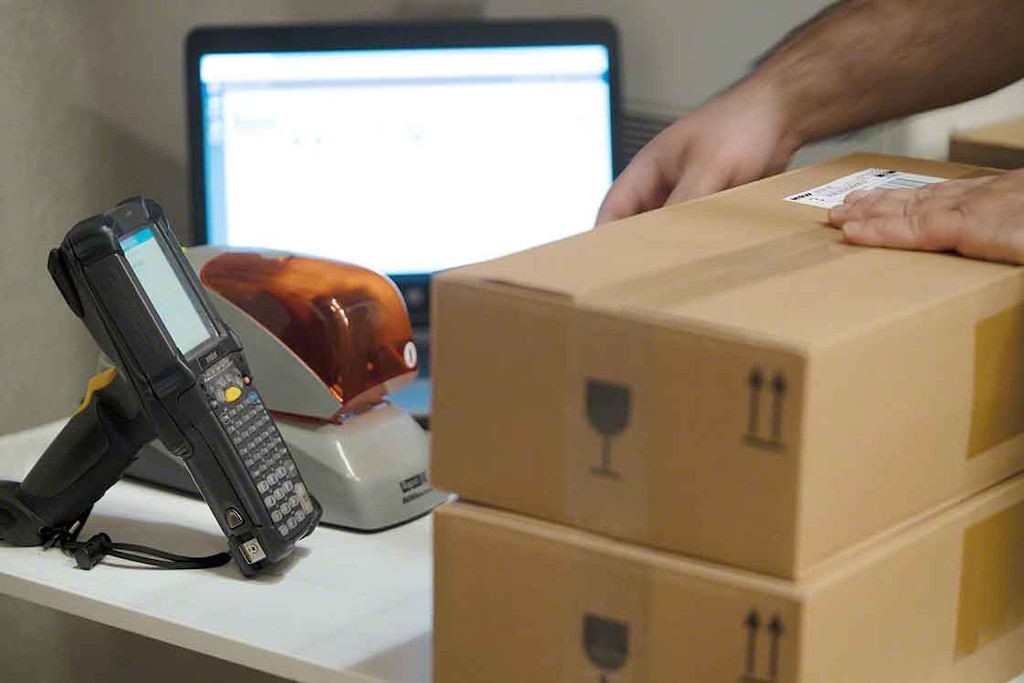
Principales despilfarros contra los que lucha Lean logistics: ¿cómo atajarlos?
Podemos clasificar los principales despilfarros en cuatro grandes grupos. Veamos en detalle sus características y cómo se podrían tratar:
- Exceso de stock almacenado
Las causas que pueden originar este aumento indebido de stock suelen ir ligadas a un exceso de producción en empresas manufactureras, pero también a una deficiente previsión de la demanda (demand forecasting).
En ocasiones, es el stock de seguridad el que se amplía bajo el pretexto de “estar cubiertos” y, al final, lo que encubre en realidad es una gestión deficiente de proveedores o una desorganización en los flujos de materiales.
Esto genera un uso de espacio en la bodega desaprovechado, que redunda en un incremento en los costos de almacenamiento y en el mantenimiento de unas existencias de baja rotación que apenas se renuevan.
¿Cómo solventarlo desde una perspectiva de Lean logistics?
Para seguir los principios de Lean logistics en esta situación, hay que trabajar, en especial, sobre aquellos factores que sí podemos controlar (frente a otros más volátiles como previsión de la demanda, por ejemplo). Algunas de las estrategias que se pueden llevar a cabo en la bodega son:
- La aplicación de la estrategia de cross-docking que limita al máximo el stock almacenado.
- La puesta en marcha del sistema just-in-time en la gestión de proveedores y en la organización de la bodega.
- El recorte de los lead time o tiempos de suministro tanto respecto a los proveedores como en los procesos intralogísticos. Esto facilitará el cálculo de las previsiones de demanda: serán más certeras cuanto más cercanas en el tiempo estén, lo que evitará descuadres por exceso de inventario.
- Tiempos de espera y cuellos de botella
La Lean logistics se basa en reducir la diferencia que hay entre el tiempo de ejecución (tiempo de trabajo que pagas a tus operarios) y el tiempo estándar (tiempo por el que cobras al cliente). El resultado de esta operación se traducirá en costos que pueden ahorrarse porque destaparán las ineficiencias.
Las causas pueden ser muy variadas y suelen estar relacionadas con un método de trabajo mal diseñado, incidencias a las que no se reacciona o desequilibrios en la carga de trabajo de cada operario.
¿Cómo solucionarlo desde el punto de vista de Lean logistics?
- Para organizar las tareas en la bodega y evitar los cuellos de botella y tiempos muertos, no hay mejor herramienta que un sistema de gestión de bodegas. Este software prepara la bodega para procesar ingentes volúmenes de información y organizarla priorizando la optimización de los procesos.
- Medir y controlar la carga de trabajo que tiene cada operario para así prevenir que unos estén parados mientras otros estén desbordados. El módulo Labor Management System para Easy WMS se ocupa precisamente de controlar este apartado.
- Para que las averías en el equipamiento no frenen la actividad de la bodega conviene contar con un plan de mantenimiento preventivo de los equipos de manutención y sistemas automáticos que se usan en la bodega como medida de prevención y, además, contar con soporte técnico para tratar de resolver la incidencia lo antes posible.
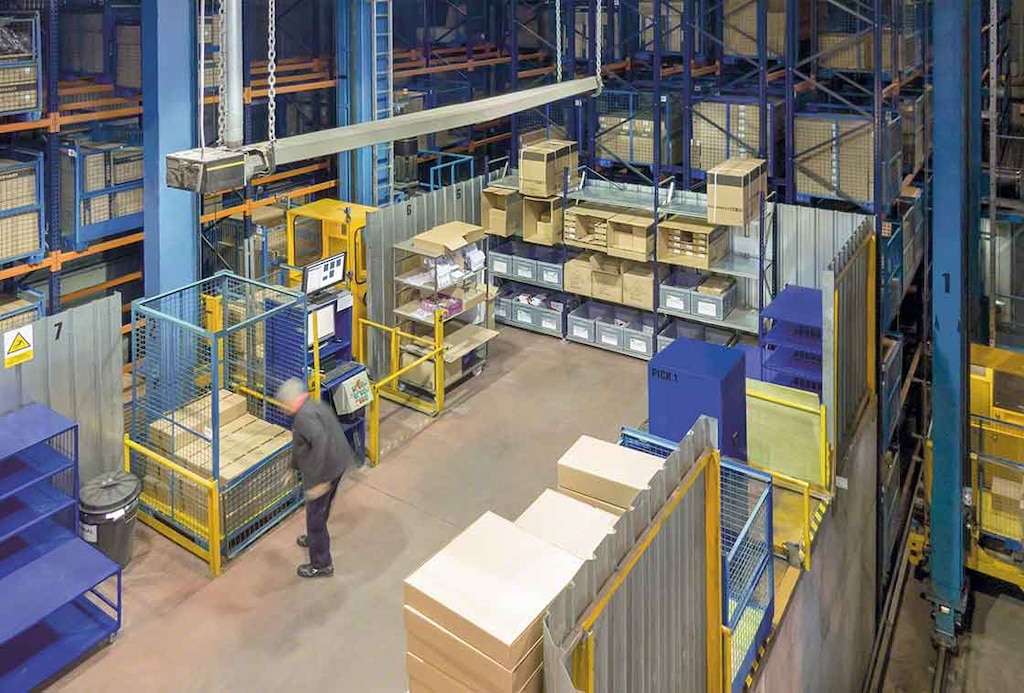
- Desplazamientos y movimientos innecesarios
Las labores de picking y preparación de pedidos en la bodega son las que mayor tiempo ocupan dentro de la actividad diaria. Por esta razón, una mala planificación de las líneas de picking puede resultar nefasto para la productividad, pues puede traducirse en desplazamientos desaprovechados (por ejemplo, usando equipos sin carga) o en el incremento de movimientos innecesarios.
¿Cómo resolverlo desde la metodología de Lean logistics?
- La automatización del manejo de cargas es una gran estrategia para reducir el tiempo dedicado a transporte intralogístico que, a la vez, permite ganar en seguridad en toda la operativa. De hecho, estos desplazamientos repetitivos suelen ser procesos para los que la automatización logra excelentes resultados. Asimismo, los transelevadores, por ejemplo, son capaces de funcionar en ciclos combinados, de forma que se aprovechan todos los movimientos llevando cargas.
- El método de picking o preparación de pedidos también influye en el despilfarro por exceso de desplazamientos. En este sentido, los WMS facilitan la organización de las rutas de picking en la bodega , priorizando la consolidación o grupaje de mercaderías y ajustando los tiempos a la planificación de expediciones.
- Errores que generan devoluciones y repetición de procesos
En general, un mayor nivel de calidad suele estar asociado a unos costos más altos, pero no siempre es así. De hecho, las mejores empresas en el sector logístico (y muchas aplican Lean logistics) se caracterizan por ofrecer un servicio excelente a un precio correcto.
¿Por qué es así? Principalmente por dos razones: porque aciertan a la primera casi siempre (y no hay que trabajar dos veces) y porque así pueden cobrar más: están respaldadas por un servicio de excepcional eficacia.
¿Cómo subsanarlos desde una perspectiva de Lean logistics?
- Si la gestión de devoluciones está complicando las operaciones en la bodega, conviene pararse a analizar las causas que las están produciendo. Si están motivadas por errores en la preparación de pedidos, de nuevo el uso de un WMS como software de picking consigue reducir drásticamente estos fallos incrementando el nivel de calidad global del servicio.
- Identificar las incidencias a tiempo es una buena práctica que puede llegar a evitar trabajar dos veces o repetir tareas.
La metodología del Lean logistics, centrada en el ahorro
El concepto de Lean logistics parte de la premisa de que el cliente, cuando compra un producto, no paga por las actividades que no agregan valor a la cadena de suministro. La metodología concentra sus esfuerzos en eliminar los despilfarros que lastran la rentabilidad de la logística en la empresa.
En Mecalux nos alineamos con nuestros clientes y trabajamos codo con codo para alcanzar sus objetivos gracias a nuestras soluciones de automatización y de software para la optimización de bodegas. Contacta con nosotros y tendrás un consultor a tu disposición para acompañarte en el camino de la logística Lean.