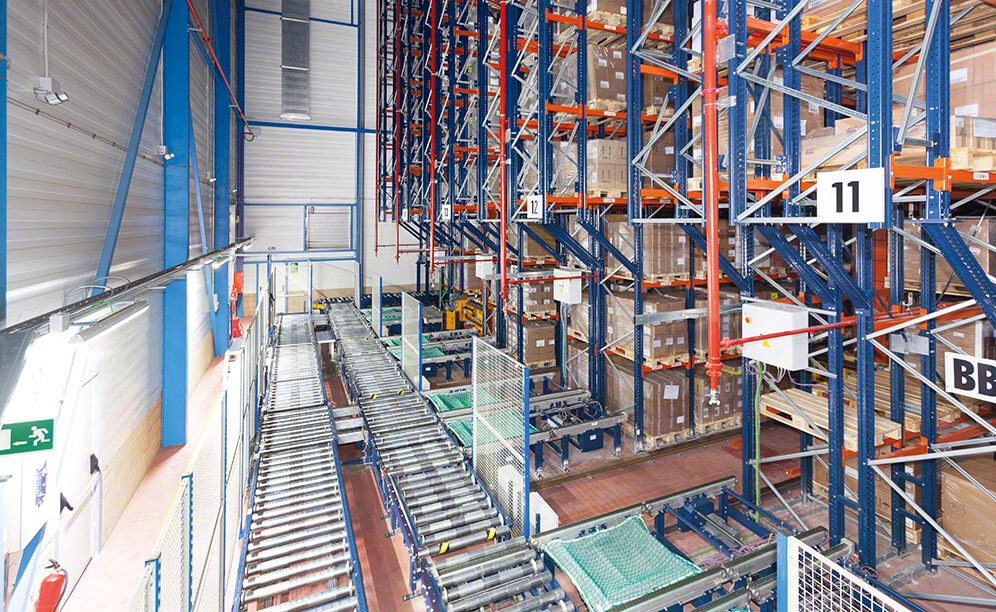
Disalfarm consigue capacidad, productividad y control con la automatización en distintas fases de su bodega
Disalfarm automatiza su bodega de forma sencilla y económica con transelevadores trilaterales
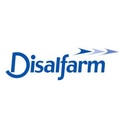
Este centro logístico ubicado en las instalaciones que Disalfarm posee en Rubí (Barcelona) ha sido edificado sobre una superficie de 39.027 m². La bodega es, totalmente automática en la actualidad y con una capacidad de almacenaje de más de 19.000 pallets, ha mejorado notablemente la productividad de la compañía. Todo ello, sin dejar de dar servicio en ningún momento durante la ampliación y modernización de la misma.
¿Quién es Disalfarm?
Disalfarm S.A. es una empresa de logística creada en España por los laboratorios Bayer, Boehringer Ingelheim y Novartis con el propósito de concentrar sus operaciones nacionales, tanto de almacenaje como de distribución de especialidades farmacéuticas.
La compañía inició su actividad en el año 2000 con la ambición de ser una empresa líder en el sector de la distribución farmacéutica. Para lograrlo, era indispensable trabajar bajo un sistema de calidad que garantizara las normas de correcta fabricación y distribución exigidas por la legislación vigente.
Hoy en día, Disalfarm dispone de una amplia gama de productos que van desde las especialidades farmacéuticas de prescripción médica, a los medicamentos de uso hospitalario, de uso veterinario, los complementos alimentarios y otros productos sanitarios.
¿Dónde está ubicada?
Disalfarm S.A. se encuentra en la ciudad de Rubí, una zona industrial próxima a Barcelona que coincide con un importante nudo de comunicaciones. Sus instalaciones están cerca de los principales centros logísticos y de distribución, lo que le permite ofrecer un ágil y rápido servicio a todos sus clientes.
Necesidades de Disalfarm: mejorar sin reducir el servicio
El crecimiento que ha experimentado Disalfarm estos últimos años ha provocado que sus necesidades de almacenaje hayan variado sustancialmente. En 2000 se erigió un centro logístico que combinaba las operaciones de almacenaje con las de picking ––menos de un 20% de los pedidos correspondían a pallets completos de una sola referencia.
En esta primera fase también se crearon dos naves dedicadas a bodega, una zona de preparación y consolidación, los muelles de carga y descarga y, por último, las oficinas y servicios. El conjunto de estas instalaciones ocupaba una superficie de 9.706 m2. Todas las estanterías de la bodega y la zona de picking fueron instaladas por Mecalux.
En 2007 la bodega propiamente dicho se quedó pequeño. El alto número de movimientos que realizaban las grúas de manutención suponía un coste desmesurado y, al mismo tiempo, aumentaba el riesgo de accidentes laborales, algo que va en contra de los principios de Disalfarm.
Ante esa situación, el gran desafío que la empresa planteó a Mecalux fue actualizar este centro logístico sin tener que alterar el servicio a sus clientes.
Punto de partida: fase 1 y fase 2
En la primera fase, que tuvo lugar en el año 2000, se construyó:
- Una bodega con capacidad para 12.900 pallets de 800 x 1.200 mm formado por diez pasillos con estanterías de 15 m de altura.
- Zona de picking compuesta por estanterías dinámicas con dispositivos pick-to-light y transportadores de cajas que comunicaban esta área con la de empaquetado y consolidación.
- Zona de picking de cajas completas que se efectúa directamente sobre los pallets.
- Bodega para productos refrigerados con capacidad para 290 pallets.
- Bodega cerrada para productos psicotrópicos.
- Nueve muelles de carga con una amplia zona de maniobra.
En la segunda fase se añadieron cinco pasillos más con racks selectivos con capacidad para 6.450 pallets, sumando un total de 19.350 pallets. Además se finalizaron tres nuevos muelles de carga.
El flujo de movimientos también se incrementó considerablemente, hasta alcanzar los 1.100 pallets al día (500 de entrada y 600 de salida). Para poder mover este número de pallets, se utilizaban los siguientes recursos:
- Siete grúas de carga frontal para trabajar en los muelles, alimentar las zonas de picking y depositar y retirar los pallets de la cabecera de los pasillos.
- Cinco grúas trilaterales para trabajar únicamente en el interior de los pasillos de almacenaje.
- 24 operarios para manejar las grúas (12 por turno).
Flujo de la mercadería en las fases 1 y 2
La mercadería llegaba a la bodega completamente paletizada. El operario leía el código de barras de cada pallet con un terminal informático y el sistema de gestión de bodegas le indicaba a qué pasillo iba asignado. Una vez determinada la posición, se utilizaban las grúas frontales para llevar los pallets hasta las ménsulas colocadas en el extremo del pasillo de almacenaje, con el fin de que las grúas trilaterales los almacenaran en las ubicaciones establecidas por el sistema de gestión.
Las operaciones de salida tenían lugar de forma inversa, con la diferencia de que la mayoría de los pallets se dirigían hacia las zonas de picking.
Fase 3: suprimir el transporte interno de pallets completos
El crecimiento de la empresa no requería un mayor número de ubicaciones, pero sí aumentar el movimiento de pallets. Para lograrlo, se barajó la posibilidad de aumentar el número de grúas y el número de operarios, con el consiguiente riesgo que eso suponía.
La instalación tenía quince pasillos de almacenaje y ya había cinco grúas trilaterales. Aunque se podían introducir cinco más, se descartó hacerlo al ser máquinas semiautomáticas y poco rápidas, el número de ciclos que ofrecían era insuficiente para cubrir las necesidades de Disalfarm.
Fue entonces, cuando Mecalux barajó dos posibles opciones relacionadas con el empleo de transportadores automáticos de rodillos y cadenas para eliminar todos los movimientos que realizaban las grúas contrapesadas dentro de la bodega.
Primera opción fase 3: descartada
La propuesta diseñaba una cabecera compuesta por los siguientes elementos:
- Dos ramales principales perpendiculares a las estanterías.
- Dos peines (uno de entrada y otro de salida) en cada uno de los pasillos de almacenaje.
- Puesto de entrada e inspección de pallets en la zona de los muelles con rechazo para los pallets no aptos.
- Salida directa hacia expediciones.
- Dos salidas a las zonas de picking.
Era la opción más coherente desde el punto de vista de cercanía con los muelles, y también era válida para poder alimentar los puestos de picking.
Para las operaciones de almacenaje se emplearían las grúas trilaterales y, en un futuro, se plantearía la necesidad de aumentar el número de grúas o buscar una solución automática. A todo esto, la parte posterior sería destinada a la zona de cambio de pasillos para las grúas trilaterales, tal y como ya estaba previsto en la primera fase.
Segunda opción fase 3: la solución
Se decidió que la parte principal de la cabecera se ubicaría en el lado posterior de la bodega. De ese modo, y como ya se venía haciendo, se dejaba el pasillo principal para las maniobras de cambio de las trilaterales y para la circulación de las grúas frontales.
Esta solución era más compleja y cara porque suponía habilitar un circuito de transportadores en la parte inferior de una de las estanterías con el fin de trasladar toda la mercadería procedente de los muelles. Lo mismo ocurría con las salidas, pero resultó ser la única solución que permitía su ejecución sin interferir en las operaciones diarias.
Los movimientos entre los peines de entrada y las ubicaciones se hacían mediante las grúas trilaterales. Cuando terminó la reconstrucción, el pasillo principal quedó habilitado solo para el cambio de pasillo de las grúas trilaterales y para las pocas salidas directas que se realizaban hacia expediciones.
A partir de ese momento, se incorporó el programa de control Galileo de Mecalux, responsable de gobernar todo el movimiento automático de los transportadores, desde el puesto de entradas hasta las salidas, pasando por la zona de picking. Los terminales de radiofrecuencia se siguieron utilizando para dar instrucciones a los operarios de las torres trilaterales.
Fase 4: automatización total de la bodega
El éxito conseguido con la automatización de los movimientos de entrada y salida hizo que, ante las nuevas previsiones de crecimiento, se planteara la posibilidad de automatizar toda la bodega.
La automatización completa comportaba un nuevo inconveniente: las máquinas automáticas (transelevadores) existentes en el mercado no permitían dejar los pallets en el nivel del suelo. Para remediarlo, la única opción viable era que el primer nivel tuviera una elevación de entre 60 y 70 cm del suelo y que se colocara una guía en la parte superior de los pasillos. Esta solución conllevaba la pérdida de todo un nivel de la bodega, o lo que es lo mismo, tener 1.290 pallets menos.
Como las necesidades de Disalfarm no consentían la pérdida de capacidad de almacenaje, tenía que encontrarse otra vía de automatización o construir otro centro logístico.
Fue entonces cuando Mecalux puso en el mercado el transelevador trilateral, sustituto natural de las grúas trilaterales, que se adaptaba perfectamente a las características que demandaba el centro logístico de Disalfarm. Sus peculiaridades son las siguientes:
- Puede dejar los pallets a solo 10 cm del suelo.
- Dispone de horquillas trilaterales en vez de las clásicas telescópicas laterales.
- No requiere de una guía en la parte superior de los pasillos, solo necesita dos guías en el suelo.
- Su altura máxima es de 15 m.
- Puede llevar un puente de transbordo (cambio de pasillos).
- También emplea Galileo como programa de control.
- Se consigue, como mínimo, la misma capacidad que con las trilaterales.
Los cambios realizados en la fase 4
Los cambios aplicados han sido mínimos y fácilmente ejecutables, principalmente:
- Instalar las dos guías del suelo.
- Modificar ligeramente las alturas entre niveles.
- Prolongar el puesto de control instalado sobre los transportadores de la cabecera.
- Colocar cerramientos de seguridad para adecuar toda la instalación a las normas respecto a la automatización de la bodega, en especial relacionadas con la seguridad dentro de los pasillos donde operan los transelevadores.
Los accesos a los pasillos relacionados con las operaciones de mantenimiento de la bodega se efectúan por el lado contrario a la cabecera, es decir, por donde estaba el pasillo principal de la instalación cuando funcionaba con las grúas trilaterales.
Para las pocas operaciones de salida de pallets completos, se ha dispuesto un canal dinámico por pasillo sobre las ménsulas que existían en la cabecera primitiva, al cual se puede acceder con grúas contrapesadas sin tener que entrar en las zonas de movimientos automáticos.
Comunicación con el software
Desde un principio, Disalfarm contaba con un sistema de gestión de almacenes (SGA) potente y adaptado a sus necesidades operativas. Seguir utilizando este sistema como base de gestión de toda la bodega era una condición obligatoria.
Por esa razón, solo ha sido necesario recurrir al programa de control estándar de Mecalux. Galileo Control System, para realizar todos los movimientos dentro de la bodega. Asimismo, se ha desarrollado una interfaz de comunicación para que ambos sistemas se comuniquen correctamente, así como una capa intermedia de gestión para evitar órdenes incongruentes de reservas y ocupación de ubicaciones.
Beneficios para Disalfarm
- Alta capacidad de almacenaje en un espacio reducido: la bodega de Disalfarm permite ubicar 19.350 pallets de 800 x 1.200 mm.
- Mejorar sin reducir el servicio: Mecalux ha optimizado el centro logístico de Disalfarm sin que la compañía haya dejado de dar servicio en ningún momento y manteniéndose en las mismas instalaciones.
- Alta productividad: la automatización de los distintos procesos de almacenaje ha incrementado el flujo de movimientos, adecuándose a las necesidades de la compañía.
- Control total: la interfaz de comunicación entre el sistema de gestión de almacenes de Disalfarm y el programa de control estándar de Mecalux posibilita gestionar todos los procesos y operativas que se producen dentro de la bodega.
Bodega de Disalfarm en Barcelona | |
---|---|
Capacidad de almacenaje: | 19.350 pallets |
Dimensiones del pallet: | 800 x 1.200 mm |
Peso máximo por palet: | 800 kg |
Altura de las estanterías: | 13 m |
Longitud de las estanterías: | 60 m |
Nº de transelevadores: | 15 |
Tipo de transelevador: | trilateral automático |
Galería
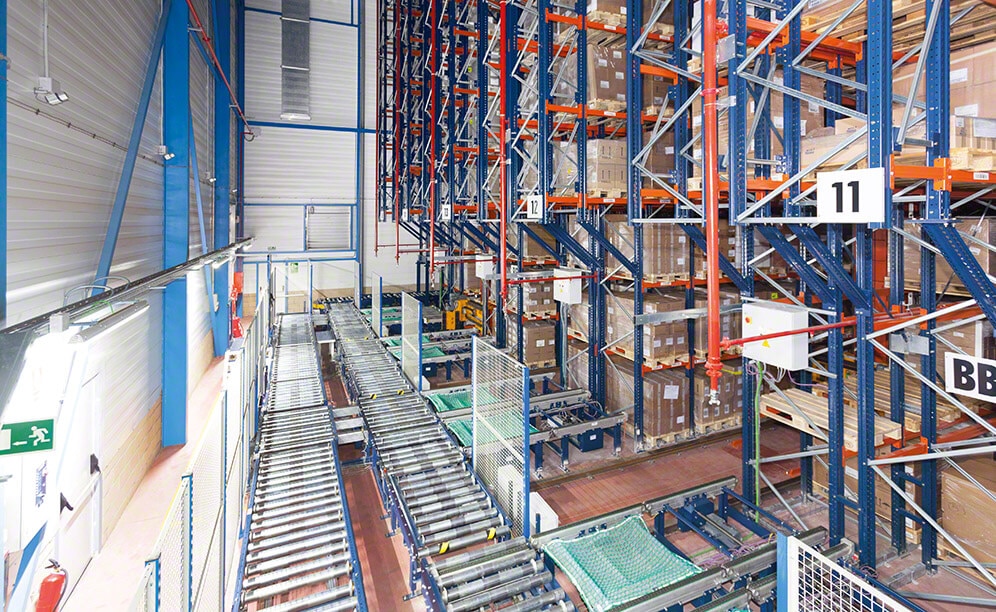
La bodega, totalmente automática en la actualidad y con una capacidad de almacenamiento de más de 19.000 pallets, ha mejorado notablemente la productividad de la compañía
Consulte con un experto