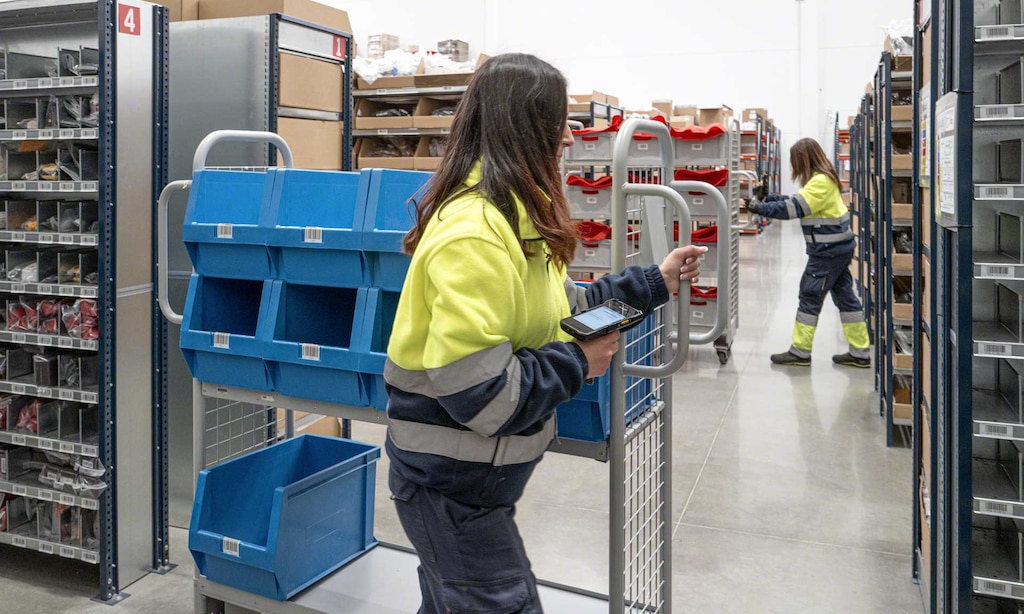
INVESTIGACIÓN LOGÍSTICA
Por Shuya Zhong, Vaggelis Giannikas, Jorge Merino, Duncan McFarlane, Cheng Jun y Shao Wei
El picking y el packing son dos procesos clave a la hora de completar pedidos. El picking supone recopilar varios artículos alojados en distintas ubicaciones de la bodega y el packing introducirlos en embalajes como cajas, bolsas o paquetes. Ambas operativas son cruciales para determinar cuánto tiempo va a pasar un pedido en las instalaciones desde que el cliente adquiere una serie de productos hasta que el envío está listo para ser despachado.
En este estudio, analizamos los resultados de planificar conjuntamente el picking y el packing en bodegas de comercio electrónico. Establecer su utilidad requiere tener en cuenta ambas tareas: mejorar una sola de estas actividades no tiene un gran impacto, ya que están intrínsecamente ligadas.
Sin embargo, y aunque se trata de dos operaciones muy vinculadas entre sí, a menudo el picking y el packing son procesos sucesivos pero independientes, llevados a cabo por dos equipos diferenciados de empleados. Proponemos que gestionar el picking y el packing de forma conjunta mejora el rendimiento de las bodegas en comparación con organizar ambas operativas por separado.
Tres preguntas clave
En nuestra investigación no buscábamos únicamente mejorar el picking y el packing, sino que también pretendíamos reducir los tiempos de espera entre ambos. Para ello se han utilizado dos métricas principales: el tiempo de tramitación del pedido (el tiempo preciso para que un solo pedido esté preparado para su despacho) y la duración del ciclo productivo (el tiempo que necesita la bodega para procesar un determinado número de pedidos hasta que estén listos para su envío).
En un bodega e-commerce, por lo general, un pedido se clasifica en una de las siguientes cuatro categorías en función de su número de referencias y de la cantidad solicitada de cada una: 1 referencia-1 artículo, 1 referencia-múltiples artículos, múltiples referencias-1 artículo y múltiples referencias-múltiples artículos. Esta clasificación afecta a las ubicaciones que hay que visitar y al tiempo de preparación y empaquetado.
La investigación también toma en consideración los distintos niveles de personal asignado al picking y al packing. A fin de evaluar los potenciales beneficios de operar de manera integrada, diseñamos un estudio experimental de una empresa de almacenaje basado en datos empíricos y comparamos la planificación conjunta del picking y el packing con la individual a través de un modelo matemático.
Gestionar el picking y el packing de forma conjunta mejora el rendimiento de las bodegas
Buscábamos dar respuesta a tres preguntas: ¿Cómo deben agruparse los pedidos para conformar una picking list? ¿Cómo deben organizarse los pickers? ¿Cómo y en qué orden deberían ser asignadas las picking lists a los encargados del packing tras completar el picking?
Para ello, fijamos las siguientes características de una bodega inspirándonos en estudios realizados sobre el tema y en las operaciones de una empresa concreta. Así, estas instalaciones funcionan con un sistema de preparación de pedidos a bajo nivel donde los productos se clasifican a la vez que se recogen. El área de picking incluye múltiples pasillos anchos y un búfer en el que cada referencia se guarda en una única ubicación. Los pickers utilizan un carrito —siempre los hay disponibles— y completan recorridos en forma de S mientras que los packers permanecen en su estación de trabajo.
Cuatro escenarios diferentes
La bodega manual estudiado es una plataforma logística que opera para un negocio minorista online. Se analizaron varios escenarios con diversos volúmenes de pedidos. Cada uno necesitaba distintas cantidades y referencias, y se dividieron también entre un número variable de picking lists.
Tiempos de espera y ejecución del picking y el packing con métodos integrados y no integrados
Si hay más packers que pickers, el ahorro de tiempo se produce antes de iniciar el picking
- Con 300 pedidos y un máximo de 24 picking lists, organizar el picking y el packing conjuntamente disminuyó el tiempo de procesamiento y la duración del ciclo productivo. A fin de lograrlo, el método integrado “sacrifica” algo de la eficiencia en el picking para lograr ahorros significativos de tiempo en la fase de packing.
- En escenarios para 100-600 pedidos distribuidos entre 8 y 48 picking lists, se muestra que a medida que la cantidad de pedidos aumenta, los beneficios de gestionar el picking y el packing juntos suelen disminuir.
- Al estudiar 300 pedidos con distintas composiciones— donde varía la proporción de 1 referencia-1 artículo, 1 referencia-múltiples artículos, múltiples referencias-1 artículo y múltiples referencias-múltiples artículos—, se observa que el método integrado impulsa el rendimiento. La ventaja es más significativa cuando la complejidad de los envíos a preparar es moderada.
- Se distribuye a doce trabajadores de diversas maneras para variar el número de pickers y packers mientras se hace frente a 300 pedidos con 24 picking lists. Cuando hay más pickers que packers, el mayor provecho de la integración reside en la reducción de tiempo antes de llegar a la fase de empaquetado. Si hay más packers que pickers, el ahorro de tiempo se produce antes de iniciar el picking. Esto supone que, en algunos escenarios en los que no se puede acelerar el empaquetado, organizar el picking y el packing conjuntamente no aporta beneficios.
Resultados: olas de picking más pequeñas
Nuestros resultados indican que la planificación conjunta de picking y packing puede optimizar el rendimiento bajo varias condiciones. Se demostró que centrarse únicamente en cambios en el picking no garantiza mejoras en todo el sistema cuando el empaquetado sigue actuando como un cuello de botella. Además, pequeños compromisos en la gestión del picking pueden generar mayores ahorros de tiempo en la fase de empaquetado e incrementar la eficiencia en general.
De igual modo, el número de pedidos considerado para la distribución del trabajo y las ventajas que la planificación conjunta puede aportar son inversamente proporcionales. Esto pone de relieve la importancia de establecer cuántos pedidos deben agruparse antes de iniciar cualquier proceso, como por ejemplo uno de picking por olas. Así, en la práctica, puede ser preferible optar por múltiples olas de menor tamaño con el fin de obtener el mayor beneficio de una planificación conjunta.
AUTORES DE LA INVESTIGACIÓN:
- SHUYA ZHONG. Profesora adjunta de Logística y Cadena de suministro en la Universidad de Bath (Reino Unido).
- VAGGELIS GIANNIKAS. Profesor de Tecnología y gestión de operaciones y director del Centro de Sistemas Inteligentes de Almacenamiento y Logística de la Universidad de Bath (Reino Unido).
- JORGE MERINO. Investigador adjunto del Instituto de Fabricación de la Universidad de Cambridge (Reino Unido).
- DUNCAN McFARLANE. Catedrático de Ingeniería de la Información Industrial en el departamento de Ingeniería de la Universidad de Cambridge y director del Laboratorio de Información Distribuida y Automatización de su Instituto de Fabricación (Reino Unido).
- JUN CHENG. Shenzhen YH Global Supply Chain Co., Ltd (China).
- WEI SHAO. Shenzhen YH Global Supply Chain Co., Ltd (China).
Publicación original:
Zhong, Shuya, Giannikas, Vaggelis, Merino, Jorge, McFarlane, Duncan, Cheng Jun, Shao Wei. 2022. "Evaluating the benefits of picking and packing planning integration in e-commerce warehouses". European Journal of Operational Research, 301 (Elsevier).
Versión de acceso libre disponible aquí.